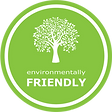
Quality Matters!

Why Quality and R&D is important for us?
At Decobite, we believe that quality is of utmost importance. We are committed to delivering products that meet or exceed our customers' expectations and adhere to the highest standards of quality. We understand that quality not only affects the satisfaction of our customers but also has a significant impact on our reputation as a producer. As such, we have implemented rigorous quality control measures at every stage of our production process to ensure that our products are of the highest quality. We continuously monitor and analyze our processes to identify areas for improvement and make necessary changes to further enhance the quality of our products. We believe that our dedication to quality sets us apart from our competitors and helps us build long-lasting relationships with our customers based on trust and reliability. For many years we spent more money and time on R&D than any producer in the market and that's the difference between us and our competitors.
Certificates




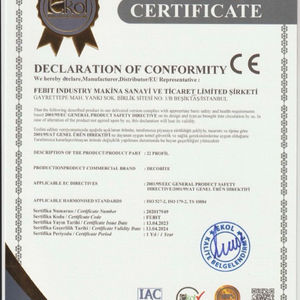


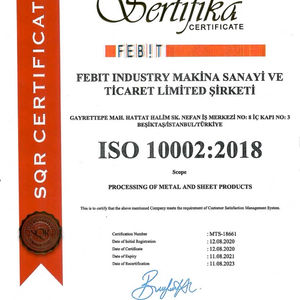
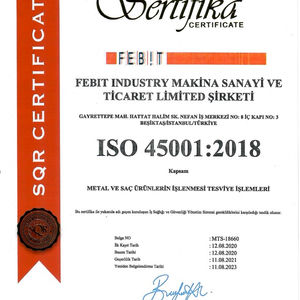
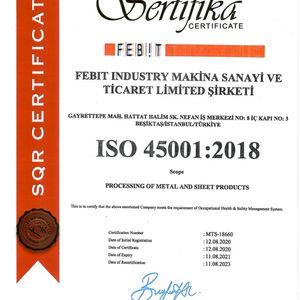
A revolutionary product!
Decobite Panels (approximately 70% Calcite which is a natural mineral material and 30% other allowed formulationsl) have been a revolutionary product in the construction industry due to their many advantages over traditional natural stone materials, such as marble or granite. Some of the ways that Decobite Panels have revolutionized the construction industry include:
-
Cost-effective: Decobite Panels are generally more cost-effective compared to traditional natural stone materials. They are typically less expensive to produce, transport, and install, which can result in significant cost savings for builders and homeowners.
-
Lightweight: Decobite Panels are lightweight and easy to handle, which makes them easier to transport and install compared to heavy natural stone materials. This can result in faster and more efficient installation, as well as lower installation costs.
-
Versatile: Decobite Panels are available in a wide range of colors, patterns, and textures, which gives designers and builders greater flexibility and freedom in their design choices. Decobite Panels can also be cut and shaped to fit a variety of surfaces and applications.
-
Durable: Decobite Panels are durable and resistant to scratches, stains, and other forms of damage. They are also moisture-resistant, which makes them ideal for use in bathrooms, kitchens, and other wet areas.
-
Easy to maintain: Decobite Panels are easy to clean and maintain, requiring only mild soap and water for cleaning. They do not require sealing or polishing like natural stone materials, which can save time and money on maintenance.

TS 10884: Coating Boards (Soffites) - Used In The Interior Surfaces Of Buildıngs - Made Of Hard Polyvinyl Chloride (PVC) – Rigid (Unplasticized) Poly(Vinyl Chloride) (PVC) Soffit
This standard covers the definition, classification and properties, sampling, inspection and tests and the form of the soffit sheet used on the interior surfaces of buildings made of rigid polyvinyl chloride.
Test Results
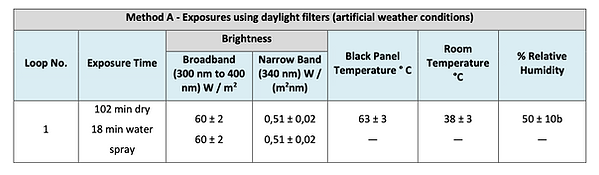

Resistance to water and humidity

Easy to clean
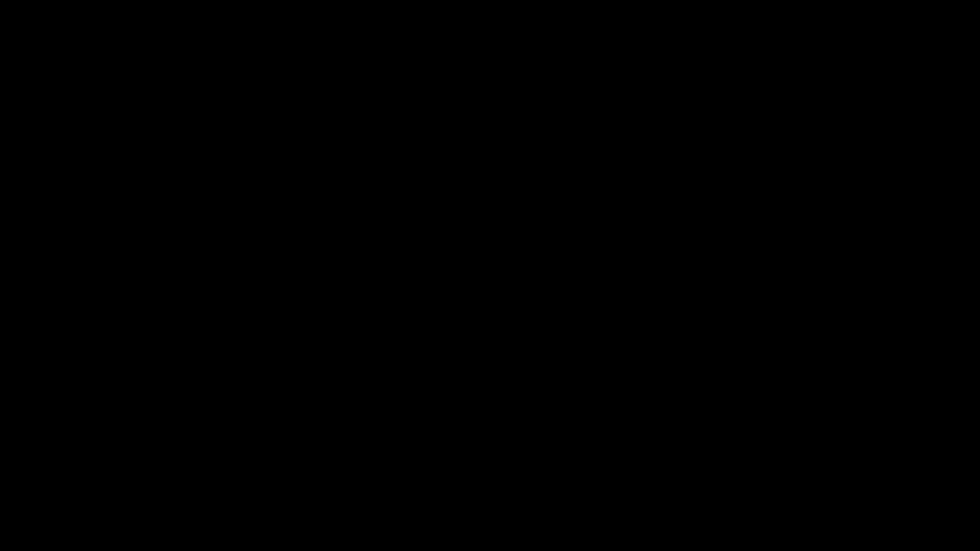
Resistance to fire
Decobite Panels (approximately 70% Calcite which is a natural mineral material and 30% other allowed formulations) are often made with fire-retardant additives that help to prevent them from catching fire or spreading flames. These additives are typically incorporated into the resin during the manufacturing process, and they work by reducing the flammability of the material.
Fire-retardant additives can be either reactive or additive. Reactive additives chemically modify the resin to make it more resistant to fire, while additive flame retardants are incorporated into the PVC material and work by releasing gases that dilute the oxygen around the flame, thereby reducing the combustion process.
Carbon Rock panels that are made with fire-retardant additives are typically rated for fire resistance according to various international standards. In the United States, for example, fire resistance is rated according to the ASTM E84 standard, which measures the material's flame spread and smoke development properties.
Overall, Carbon Rock panels with fire-retardant additives are a good choice for applications where fire safety is a concern, such as commercial buildings, hotels, and hospitals. However, it's important to note that no material can be completely fireproof, and proper fire safety measures should always be in place.
Test Results
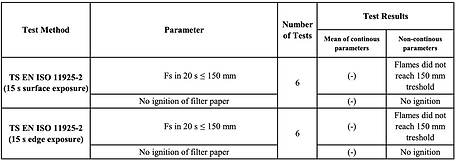

Stay Safe!
Products that are resistant to fire.
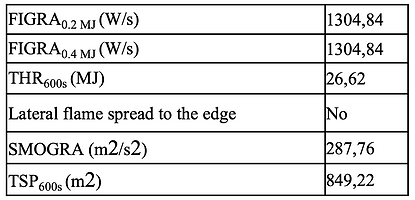
Fire Test Graphics
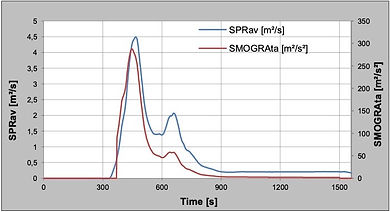


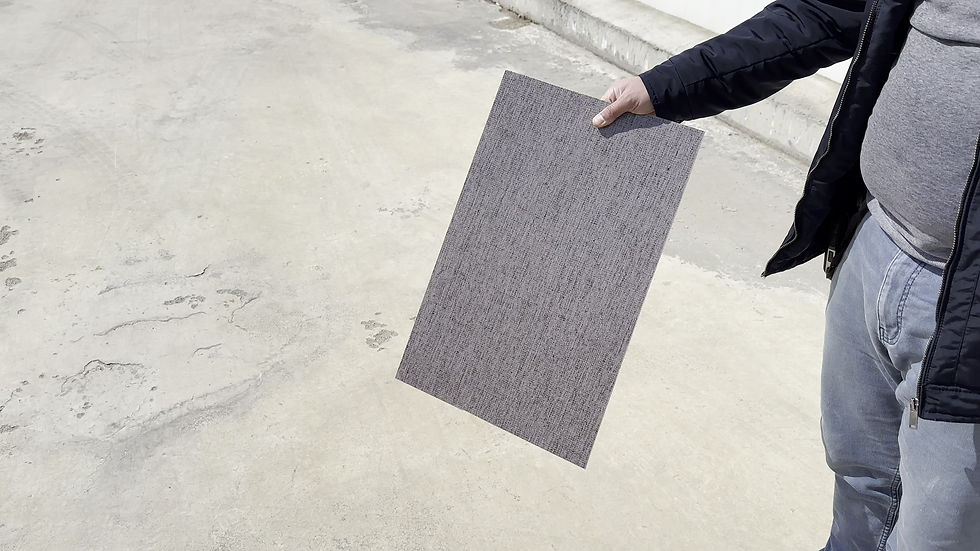
Resistant to Scratch
Decobite Panel is a type of synthetic material used for various applications such as interior decoration, furniture, and wall cladding. It is made by combining PVC (polyvinyl chloride) resin with marble dust and other additives to create a material that mimics the appearance of natural marble.
Resistant to Scratch properties are an important consideration for Decobite Panel products, especially in high-traffic areas. Decobite Panels can be treated with a special coating that makes them resistant to scratches, scuffs, and other types of surface damage. This coating is typically made from a combination of chemicals that provide a hard, durable layer on top of the Panels.
Resistant to Scratch Decobite Panels are ideal for use in areas such as restaurants, hotels, hospitals, and schools, where they are likely to be subjected to frequent wear and tear. They are also popular in residential settings, where they can be used for flooring, wall panels, and other decorative applications.
To maintain the Resistant to Scratch properties of Decobite Panels, it is important to avoid using abrasive cleaning materials or tools, as these can damage the surface of the material. Instead, it is recommended to clean Decobite Panels with a soft cloth and a mild cleaning solution.

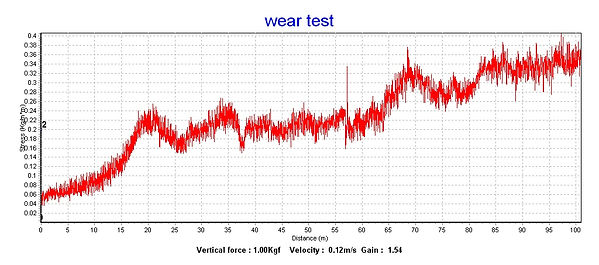

Keep it Quiet!
And Also Resistant to Sound and Vibration.
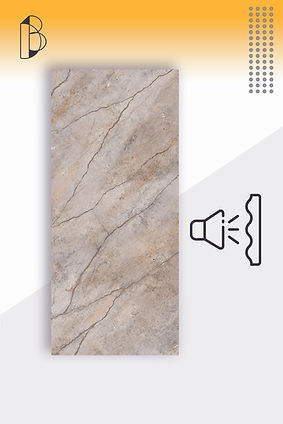

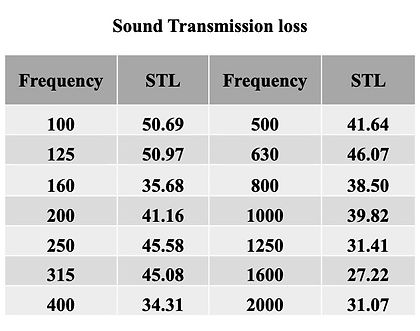
Test Results


Decobite Panels (approximately 70% Calcite which is a natural mineral material and 30% other allowed formulations) are known for their high strength and durability, which makes them a popular choice for interior decoration, wall cladding, and other applications. Carbon Rock panels are made by combining resin with calcium carbonate and other additives, which create a material that is both lightweight and strong.
Here are some of the key properties that make Carbon Rock Panels high strength:
-
Impact resistance: Carbon Rock Panels have a high resistance to impact, which means they can withstand heavy use without cracking or breaking.
-
Moisture resistance: Carbon Rock Panels are resistant to moisture, which makes them ideal for use in areas such as bathrooms, kitchens, and other wet areas.
-
Scratch resistance: Carbon Rock Panels have a hard surface that is resistant to scratches and abrasions, which helps to maintain their appearance and durability over time.
-
Fire resistance: Carbon Rock Panels are typically made with fire-retardant additives, which help to prevent them from catching fire or spreading flames.
-
UV resistance: Carbon Rock Panels are resistant to UV radiation, which means they will not fade or discolor over time when exposed to sunlight.
Powerful
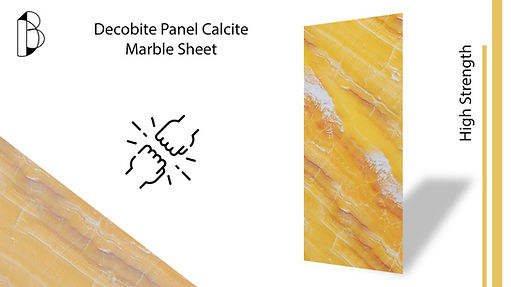
ISO 527-2: Plastics - Determination of tensile properties - Part 2:Test conditions for moulding and extrusion plastics
This part of ISO 527 specifies the test conditions for determining the tensile properties of molding and extrusion compounds on the basis of the principles from ISO 527-1. The methods are applied using specimens which may be either moulded to the chosen dimensions or machined, cut or punched from injection or compression-moulded plates. The multipurpose test specimen is preferred.
Test Results


A Product With Impact strength.
Decobite Panels (approximately 70% Calcite which is a natural mineral material and 30% other allowed formulations) are known for their high resistance to impact, which means they can withstand heavy use without cracking or breaking. This makes them a popular choice for applications where durability is important, such as interior decoration, wall cladding, and other decorative purposes.
The high impact resistance of Carbon Rock Panels is due to the material's unique composition. Carbon Rock Panels are made by combining resin with calcium carbonate and other additives, which create a material that is both lightweight and strong. The calcium carbonate provides a high level of hardness and strength to the material, while the resin gives it flexibility and impact resistance.
Solid Rock!
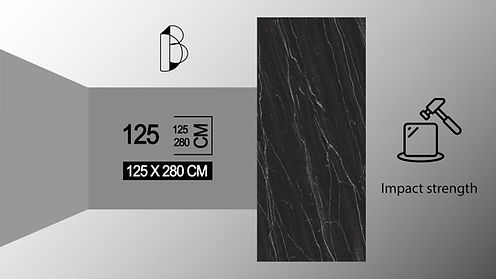
ISO 179-2: Plastics- Determination of Charpy Impact Properties- Part 2: Instrumented impact test
This part of ISO 179 specifies a method for determining Charpy impact properties of plastics from force deflection diagrams. Different types of rod-shaped test specimen and test configuration, as well as test parameters depending on the type of material, the type of test specimen and the type of notch are defined in part 1 of ISO 179.
Test Results

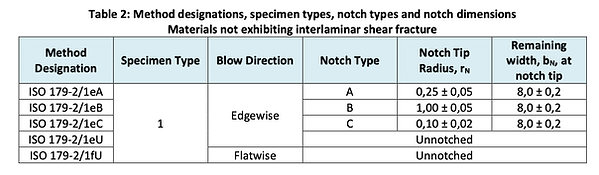
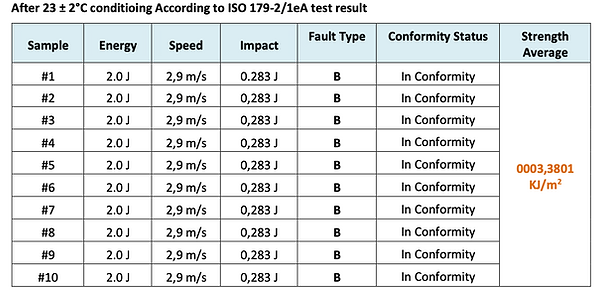
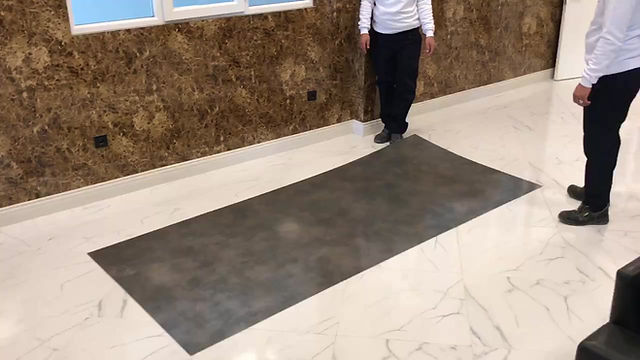

